Analyzing and ensuring the quality of 3D-printed components
Applied analyses:
- Fourier-transform infrared spectroscopy (FTIR)
- Light microscopy
- Nanoindentation
- SEM/EDX Analysis
- X-ray fluorescence analysis (XRF)
- X-ray inspection
- Microsectioning and Ion beam etching
- Particle size analysis
The capabilities of additive manufacturing (AM for short, also known as 3D-printing) have increased in the past years exponentially, ranging from organic to ceramic to metallic materials. AM covers almost the entire spectrum of serial production. These days, modern systems can achieve quantities that easily match those of industrial production lines, in a constantly expanding market moving towards serial manufacturing. The big advantages of additive manufacturing are its degrees of flexibility in terms of the geometry and complexity of components. Nearly every shape can be produced, which even the most up to date subtractive methods can either only manufacture at great cost or can’t manufacture at all.
As AM processes are seeing more and more usage in sensitive and critical to security areas, such as medical technologies and the aerospatial industry, quality ensuring processes are becoming similarly important. A precise analysis, should damage come to pass, is more often than not the best way to improve product reliability or to better understand the processes involved.
This makes having a powerful and efficient partner, who supports manufacturers of 3D-printed components with the best possible support in terms of analytical expertise, all the more important. The HTV Conservation GmbH’s Institute of Material Analysis provides every supplier of additively manufactured components with a full spectrum of analytics to ensure the best possible quality, as well as full support in terms of optimizing the manufacturing processes.

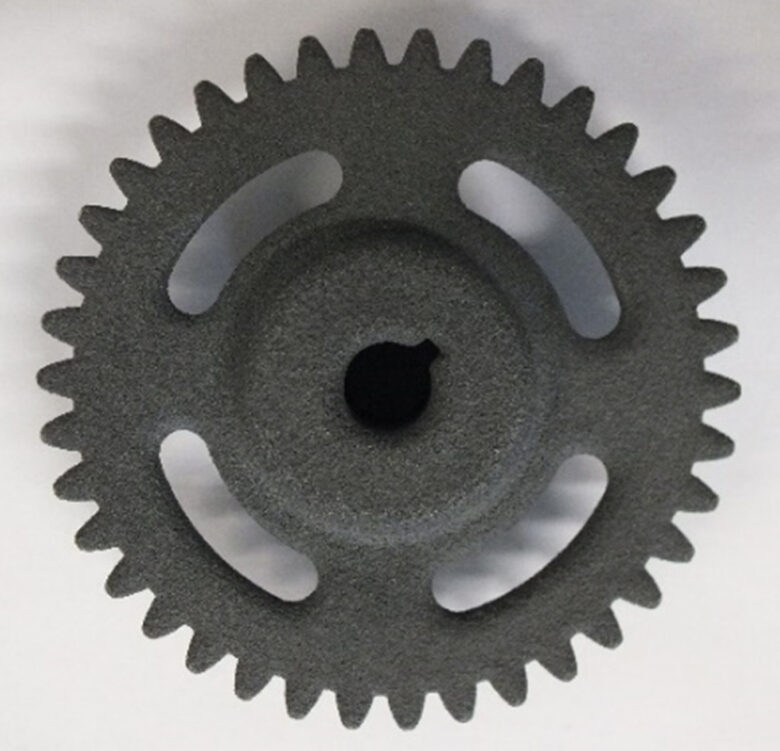
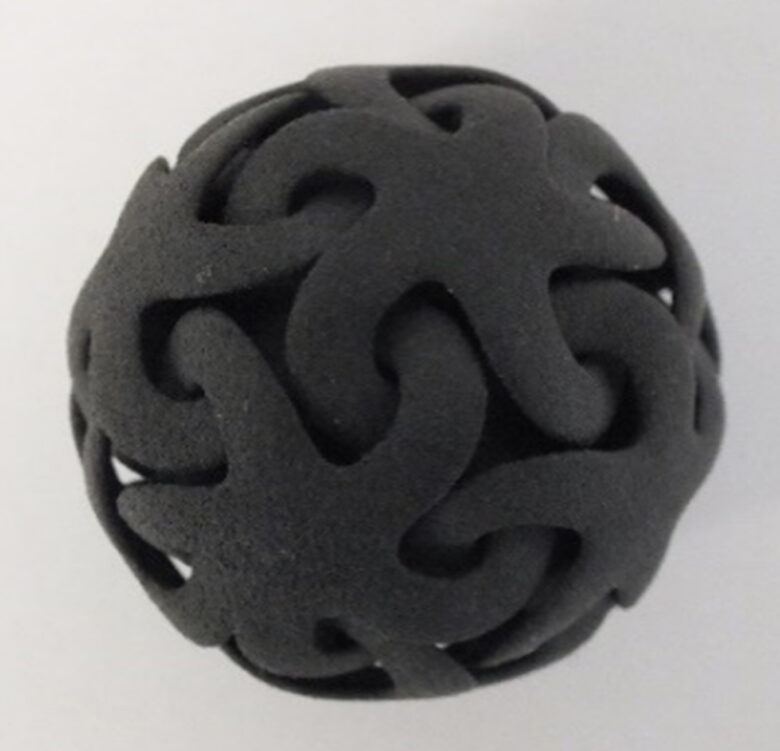
X-rays tracking down the defect
The HTV Conservation’s state of the art µCT x-ray devices allow for a non-invasive analysis of a component’s microstructure to unveil even the smallest defect. This way it is possible to more rapidly identify eventual weak spots and adjust the process parameters before a complaint from the customer’s side.
In this way, structures can be measured to ascertain their exact position inside the component, which allows for more precise backtracing of the causes of defects, so those can be eliminated during the process optimization. It can also be ascertained which kind of irregularity is present inside the component, such as an inclusion, a pore or a void, which is very useful during troubleshooting.
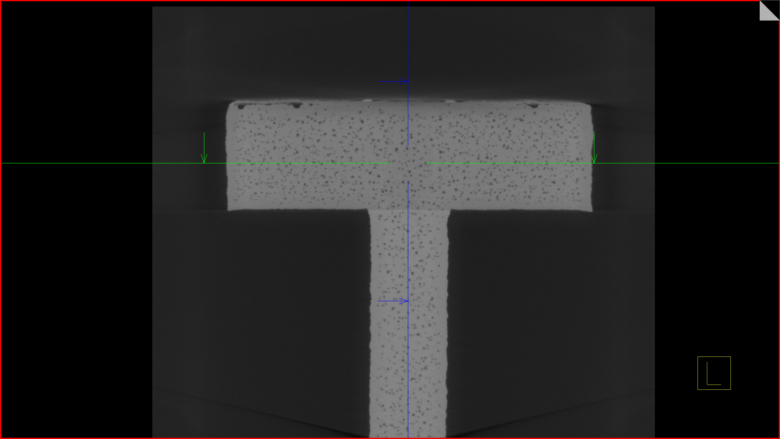

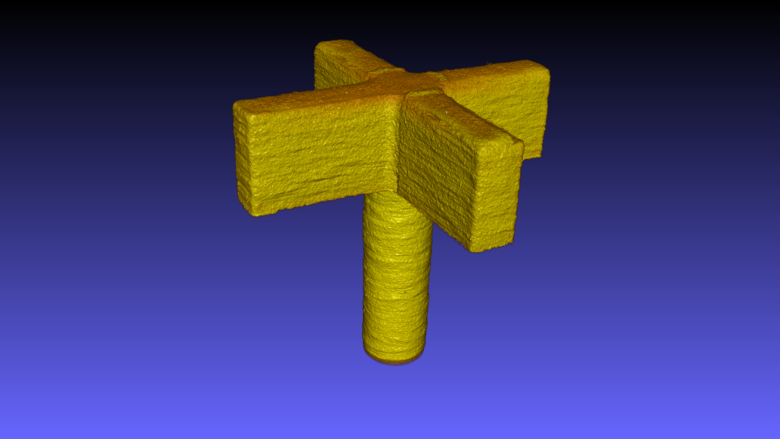
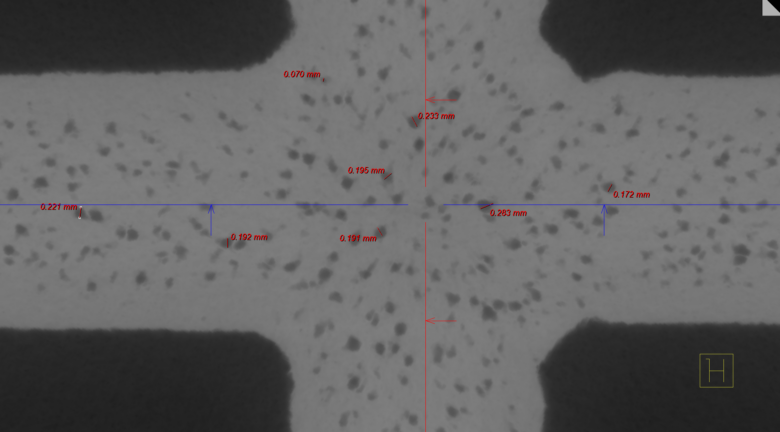

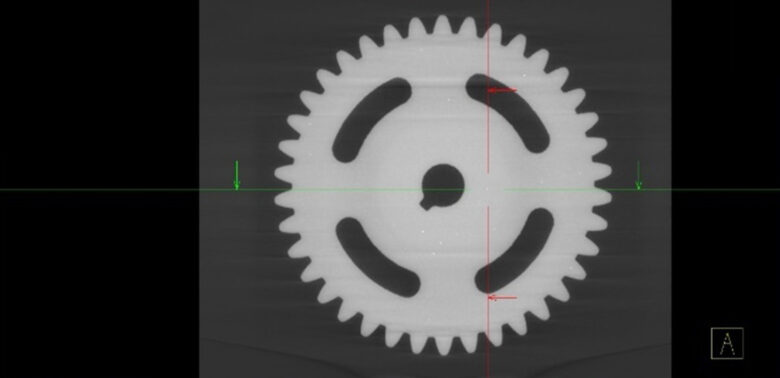
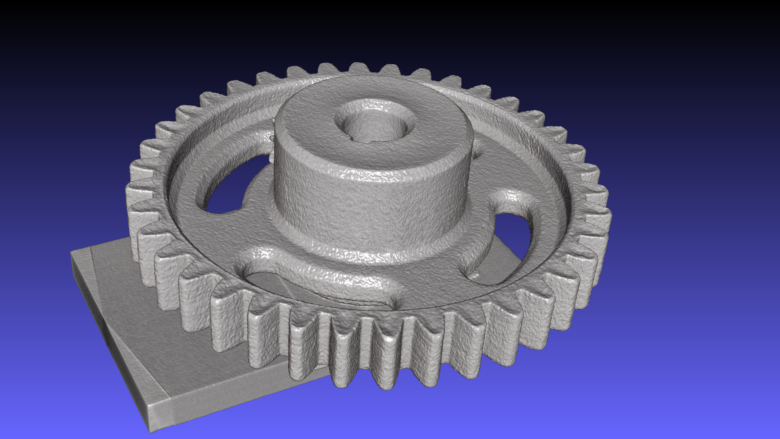
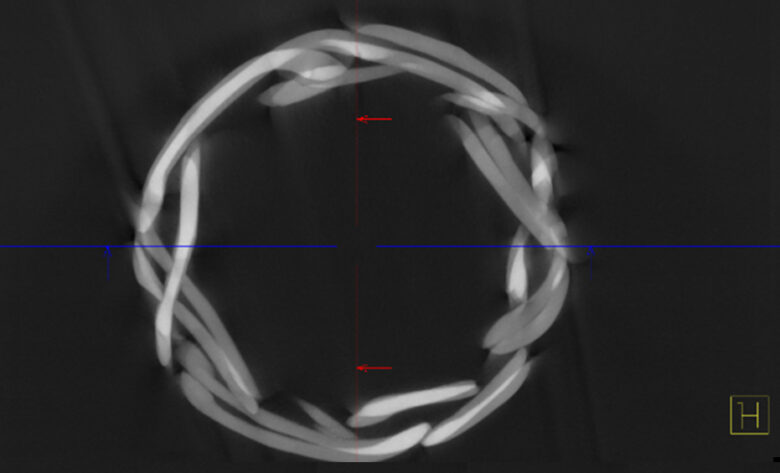
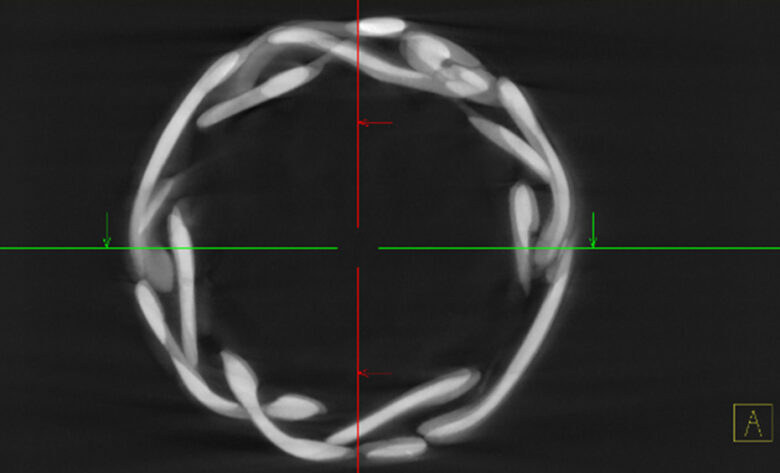
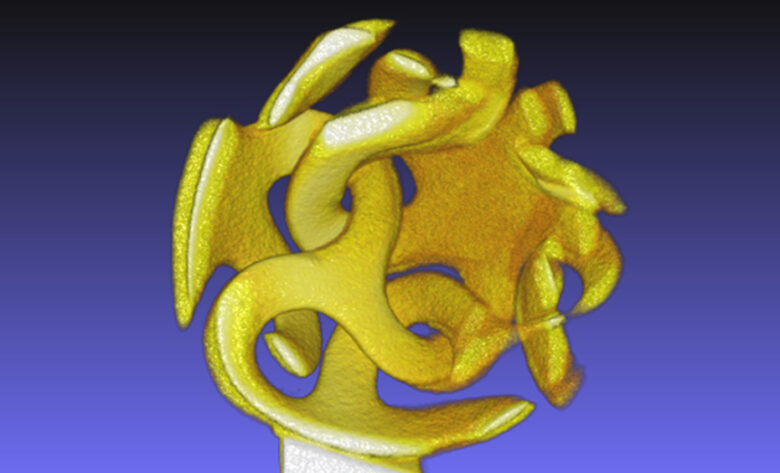
Spectroscopy, metallography and microscopy for better quality
The quality of the base material is essential for the quality of the final product. Plastic materials may contain unwanted additives which can influence the mechanical behavior of the additively manufactured component. Choosing the right plastic material is just as essential for the qualities of the final product. Using their Fourier-transform infrared spectroscopy (FTIR), the HTV Conservation GmbH can indentify plastic materials and uncover possible, unwanted additives. This ensures a base material quality corresponding to the customer’s quality requirements. Aging processes may also be documented using FTIR spectroscopy, which can be vital in a defect analysis.
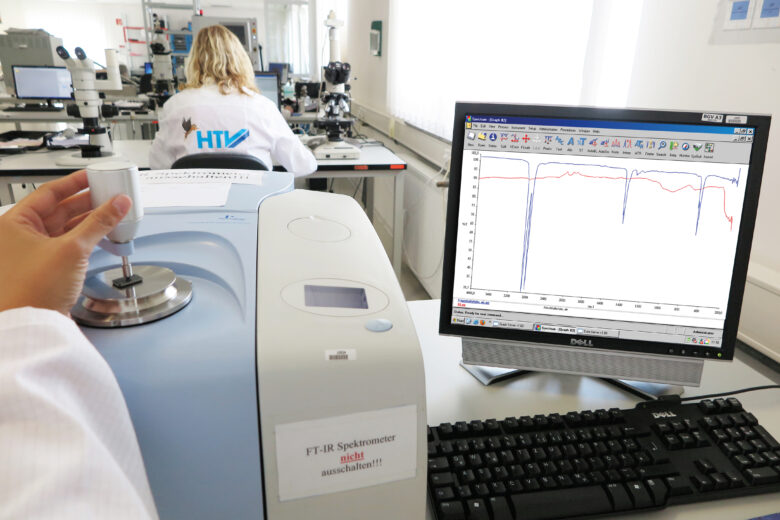
For metal-based additive manufacturing the quality of the base powder can be analyzed using metallographic methods to uncover irregularities, such as pores in the metallic particles. Said pores can negatively impact the component’s quality further along in the process.
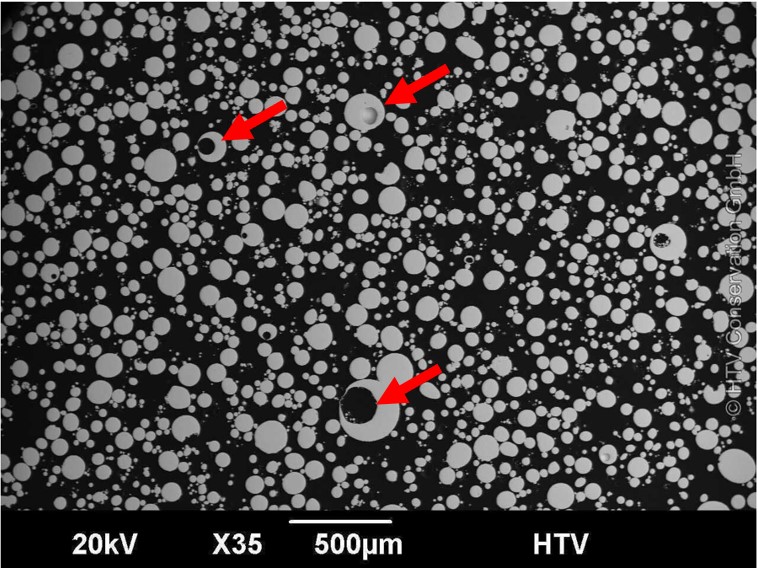
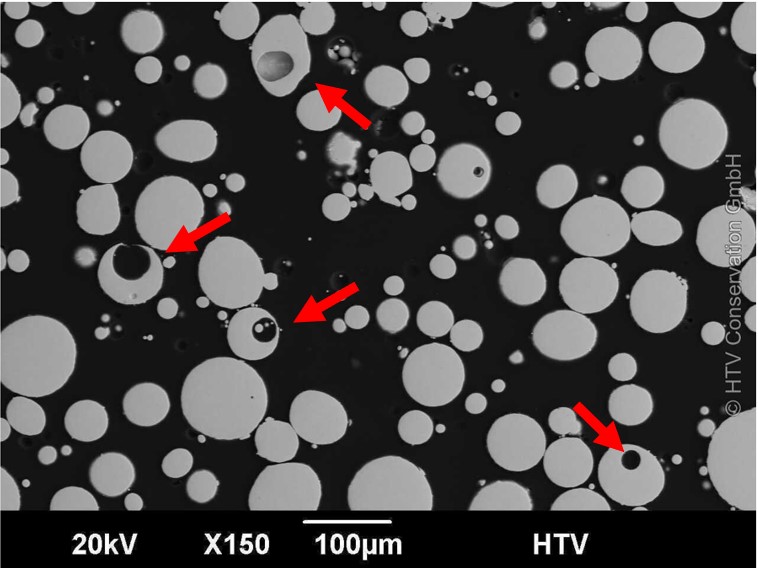
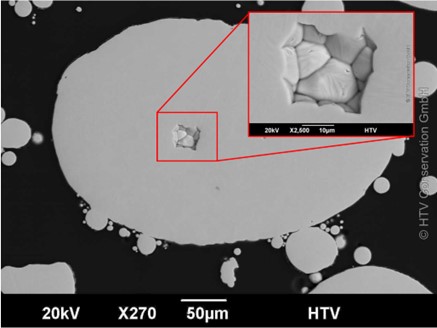
Particle size analysis on powders for additive manufacturing
The composition of powder particles can be analyzed using scanning electron microscopy (SEM) and energy-dispersive x-ray spectroscopy (EDX). State of the art light microscopic and scanning electron microscopic analyses measure the particle size distribution which can also have an essential influence on the final quality of the printed product.
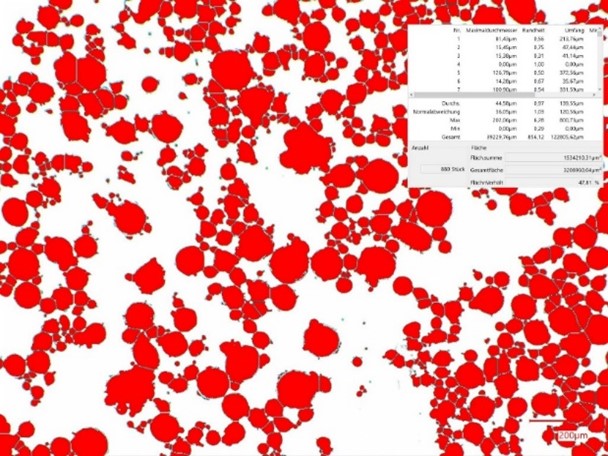
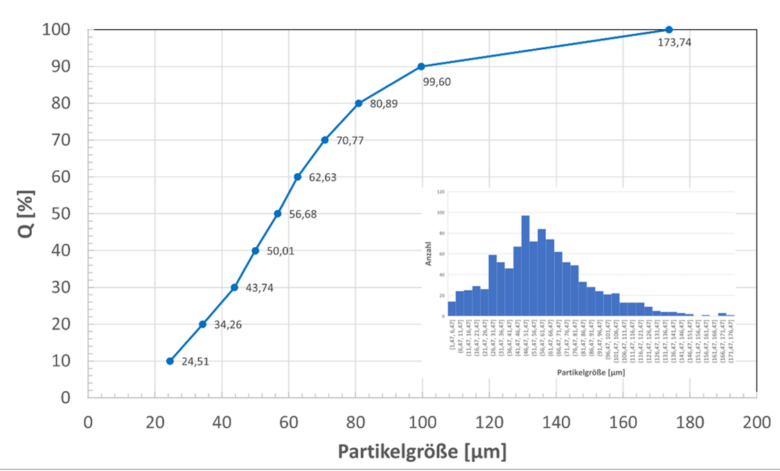
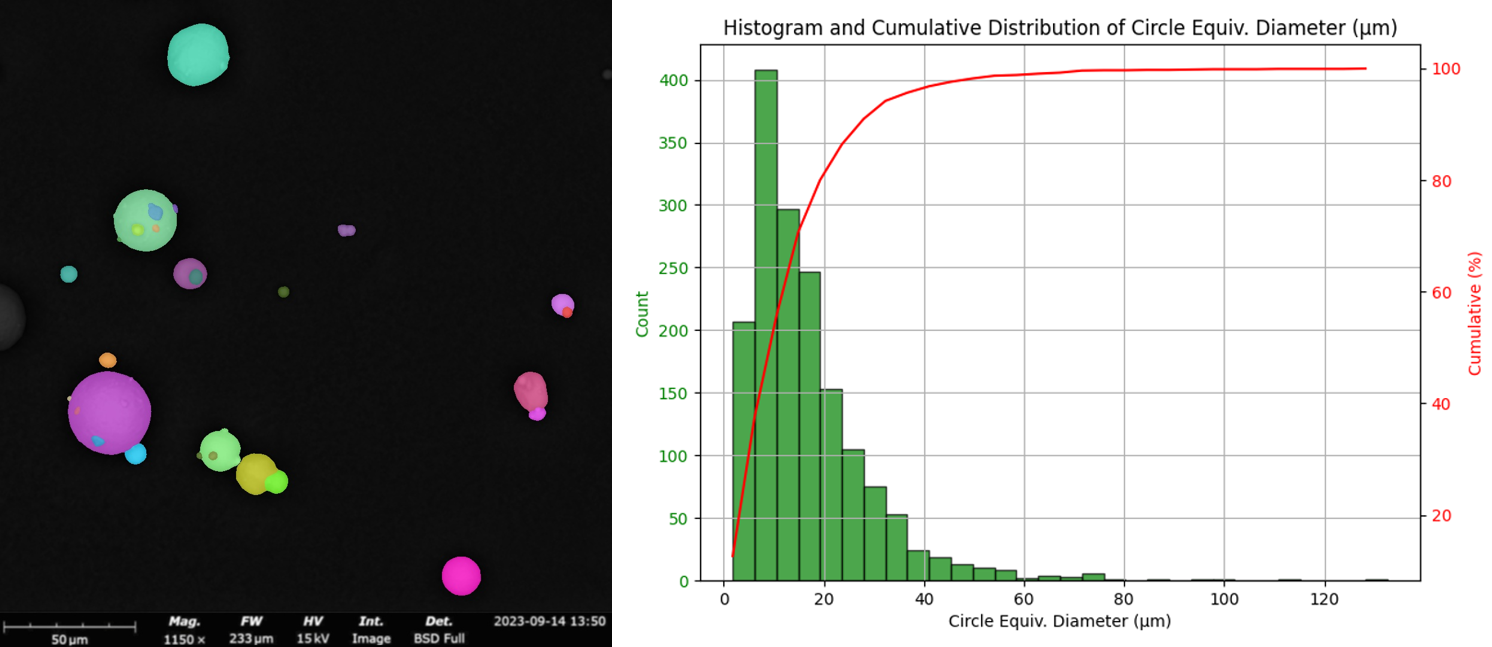
In order to fully exploit the advantages of additive manufacturing, such as producing complex and yet highly specific components or recreating a discontinued replacement component no longer available on the open market, it is of vital importance to ensure that these costly manufactured products match all the necessary quality and reliability requirements. The HTV Conservation GmbH’s material testing provides every possible support in evaluating and documenting the quality of 3D-printed components. With the help of the HTV Conservation, manufacturers can ensure the quality required by their customers.