BGA-Reballing
HTV-Reballing is used among other things for:
- Replacing defective or deformed balls (such as those affected by tests or contacts)
- Ball renewal of components after desoldering them from a printed circuit board
- RoHS standard rework from leaded to lead-free
- MIL-spec standard rework from lead-free to leaded, should there be a shortage of leaded components
Ball Grid Array components, BGA for short, are very complex yet ever more employed components. Given the arraignment of the contacts on the underside of the component and with a greater number of contacts by smaller dimensions in comparison to other package forms like QFN or TSOP, BGAs see a preferred usage in FPGAs or huge controllers with several hundred interfaces. The advantage in necessary space however is offset by a much more sensitive soldering process. A less than ideal soldering, over-laid or wrongly laid components will cause the solder balls to have a less than ideal connection with the printed circuit board, a phenomenon which is also known as the head-in-pillow defect.
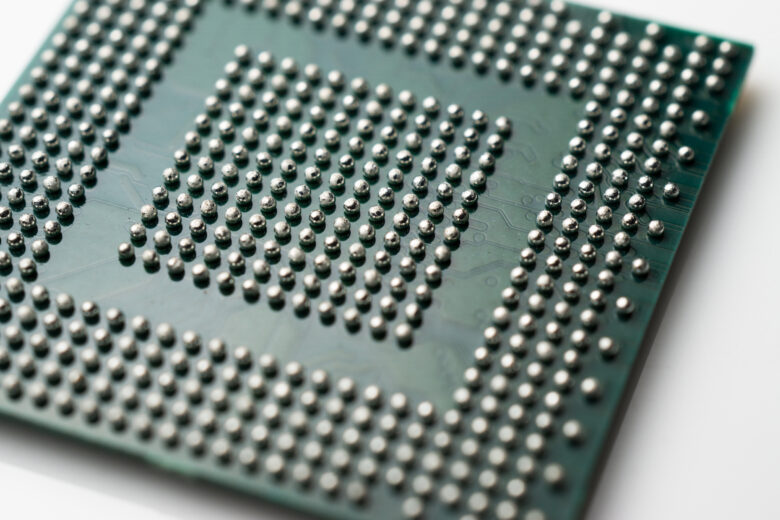
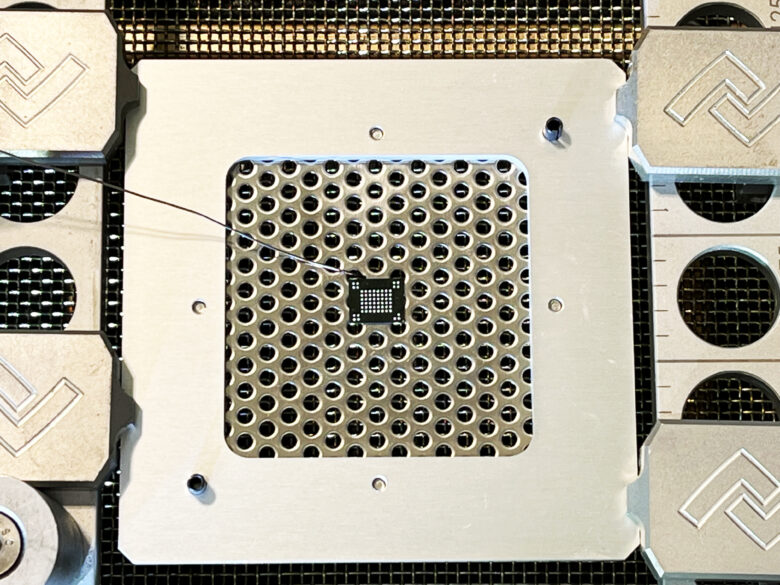
During reballing, meaning the renewal of the BGA’s solder balls, the previous solder balls are removed and replaced with newer balls. It is both possible to renew the not properly wetting balls or the balls which impede the soldering process, as well as completely re-alloy the balls from leaded to lead-free (and vice versa).
This can be done from both tray or tape. Depending on the individual customer requirements the return delivery may also be performed on the arrival trays or taped & reeled. Quantities of up to 50 pieces can be treated in the HTV fastlane.
Reworking printed circuit boards more often than not requires reballing if it concerns the renewal of defective solder connections or if, say, components were not properly assembled and require a crossover exchange.
Once a specialized rework device has desoldered the component in question from the assembly, both the component and the printed circuit board are then thoroughly cleaned and all possible traces of tin are removed from that specific area. Following the actual reballing, the component is then transferred back to the rework device, where the balls are fused completely onto the component using a two-sided heat treatment. This process is documented using a high resolution camera to immediately counteract any possible errors.
The HTV sales team stands at the ready to offer every customer an individual and non-committal price quote.