Component programming in one of the globe’s most efficient and powerful programming centers
HTV offers multiple services of German ingenuity regarding component programming:
- Programming/Flashing of:
- Microcontrollers, flash memories, EEPROMs, EPROMs, GALs, PALs, FPGAs, EPLDs, OTPs, etc.
- Memory cards (SD-Card, Micro-SD, Compact-Flash, etc.)
- Huge NAND-Flashes via the unique Huge Memory Flashing HMF according to the SmartJET Highspeed-Technology
- Special components (e.g. configuration data for HAL sensors)
- Discontinued component types
- Complex serial numbers (e.g. also special solutions like several serial numbers in one component)
- Wafers or ASICs
- SoMs (System on Module, such as ESP32-modules like the ESP32-WROVER etc.)
- In-house adaptor and algorithm development
- In-house development of software tools for data processing within special solutions
- HTV-On-Site Programming – Programming by HTV directly at the customer’s location
- Further services:
- 3D-Lead Inspection, marking as well as taping and reeling
- OTP-Alive method to reprogram components which normally could only be programmed one time (OTP)
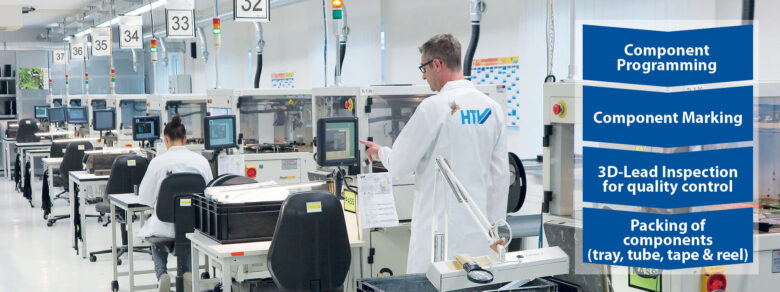
HTV posesses a programming capacity of more than 750,000 pieces per day.
Fast sample production, short processing times as well as express service make it possible to deliver the customer’s programmed goods within a few work days or even within hours. A special department for adapter and algorithm development enables to adjust new component types or ASICs and packages to the programming systems, mostly without long lead times, and to perform the programming for mass production with customer software. Due to in-house maintenance and calibration of older programming systems, HTV also offers the programming of many obsolete device types already discontinued by the manufacturer. On request, the programmed customer software can be archived and stored on secure HTV servers for up to 15 years. Thus, older software versions are available at any time if required.
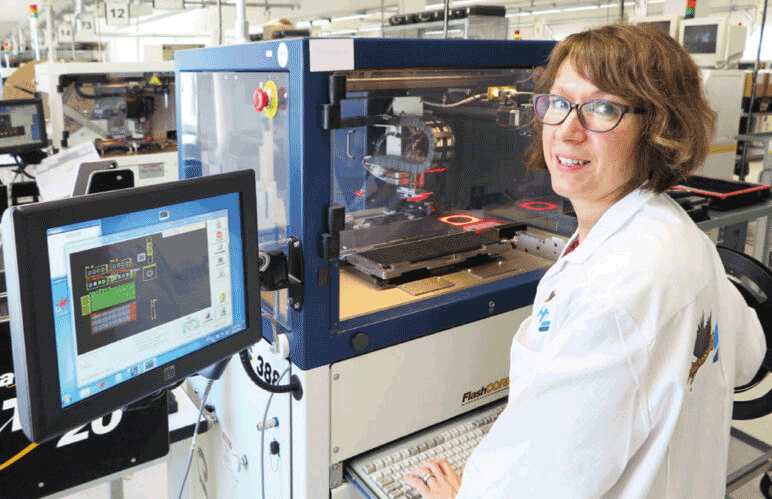
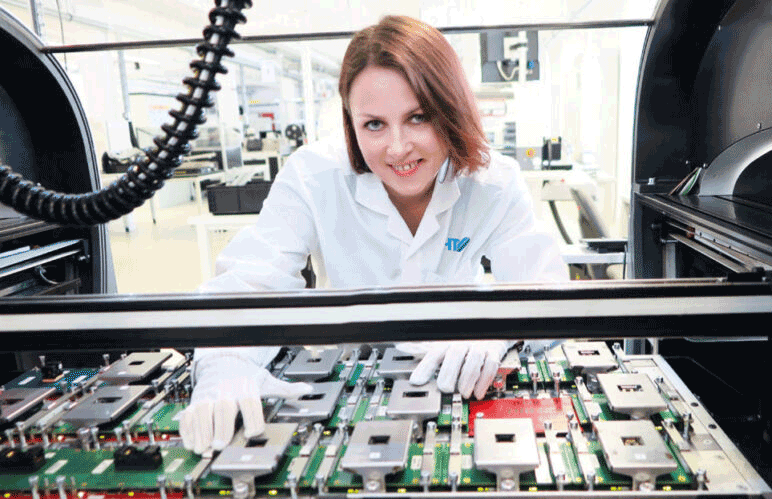
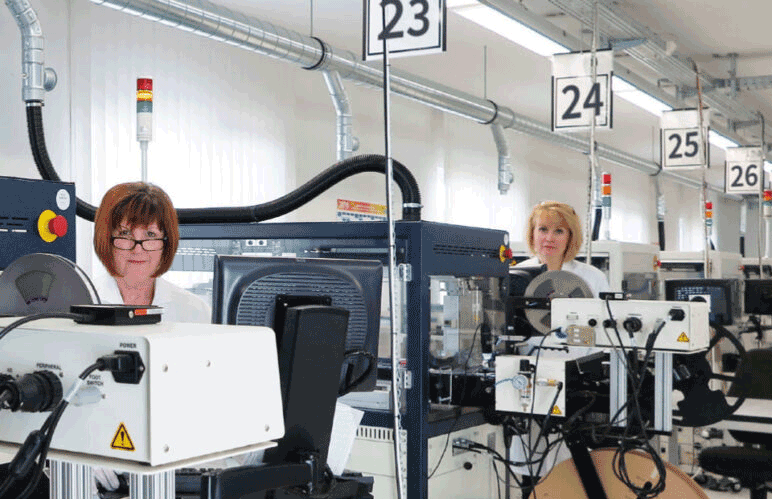
Process reliability and quality control
As a global provider for a majority of the automotive suppliers and manufacturers all processes are adjusted to the appropriate standards, ensuring the components are processed according to the 0 ppm-target. Thus, the certification according to quality management standard ISO 9001 is mandatory. Barcode controlled processes serve to precisely assign customer software and therefore provide a 100 % traceability of components, machines and operators as well as the preventive maintenance of the equipment. Before shipping the processed goods, all components and working papers are subjected to a detailed final visual inspection.
Failure analysis
If problems or failures occur during programming, these can be analyzed immediately in detail. As one of the world‘s leading test houses, HTV has extensive resourcefulness and equipment to determine, document and evaluate failure causes comprehensively. The provision of a detailed examination report enables the customer to instantly initiate the further necessary steps.
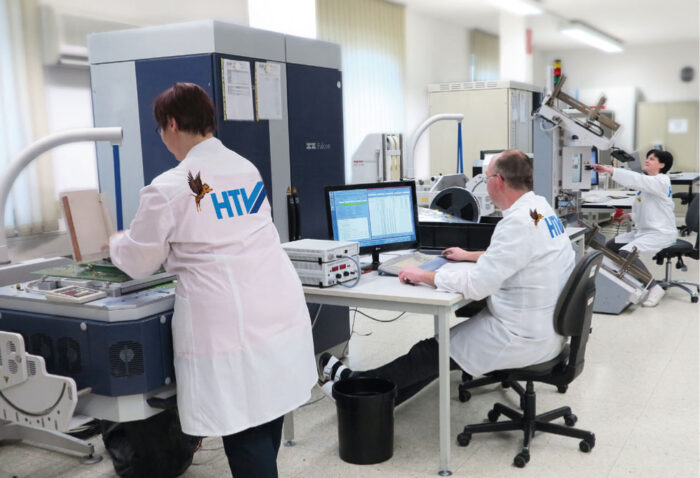
Subsequent services

Components are labelled or marked directly after programming. This can be done by laser, label or color dot. An applied works number and the programming date, for example, enable to make the programmed software version externally visible and ensure 100 % traceability.

After programming and marking the component, the 3D lead inspection is performed for quality control purposes. Using a three-dimensional process, all mechanical component parameters are measured with high precision according to the data sheet. Automated optical inspection systems also check both the component labeling and the component position.
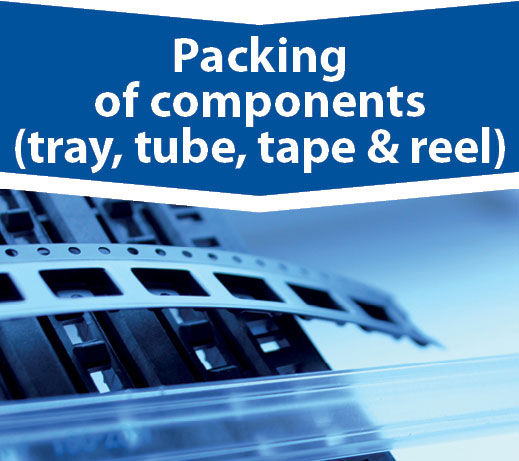
In conclusion, the components are packed according to customer requirements (tray, tube, tape & reel).
Process flow of component programming
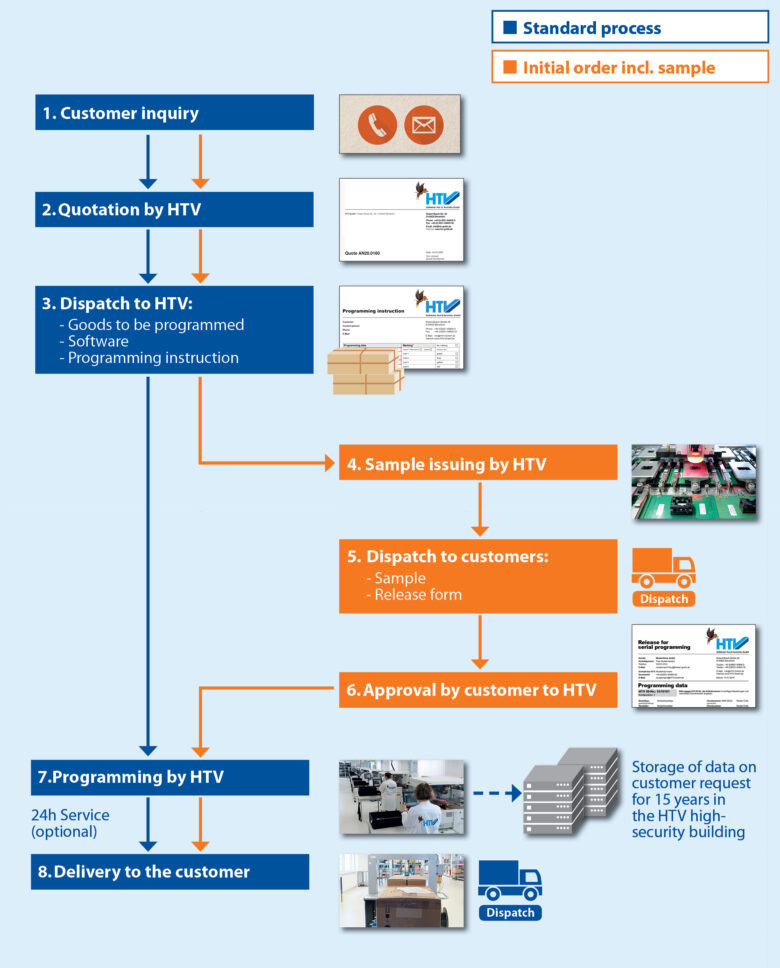
HTV-On-Site Programming
With On-Site Programming HTV offers its customers the possibility of programming components directly at the individual customer’s location. In doing so, all necessary machines as well as the personnel – also in case of possible capacity expansions – are provided by HTV. The customer thus benefits from the advantages of an in-house programming without investment, personnel or maintenance costs. Should the end customer require extremely large quantities at short notice, HTV can compensate for the increased demand by providing additional machine capacity at the site in Bensheim.